Our BGA rework and reballing services offer precision and reliability for correcting PCB assembly issues. Ensure strong connections and consistent performance.
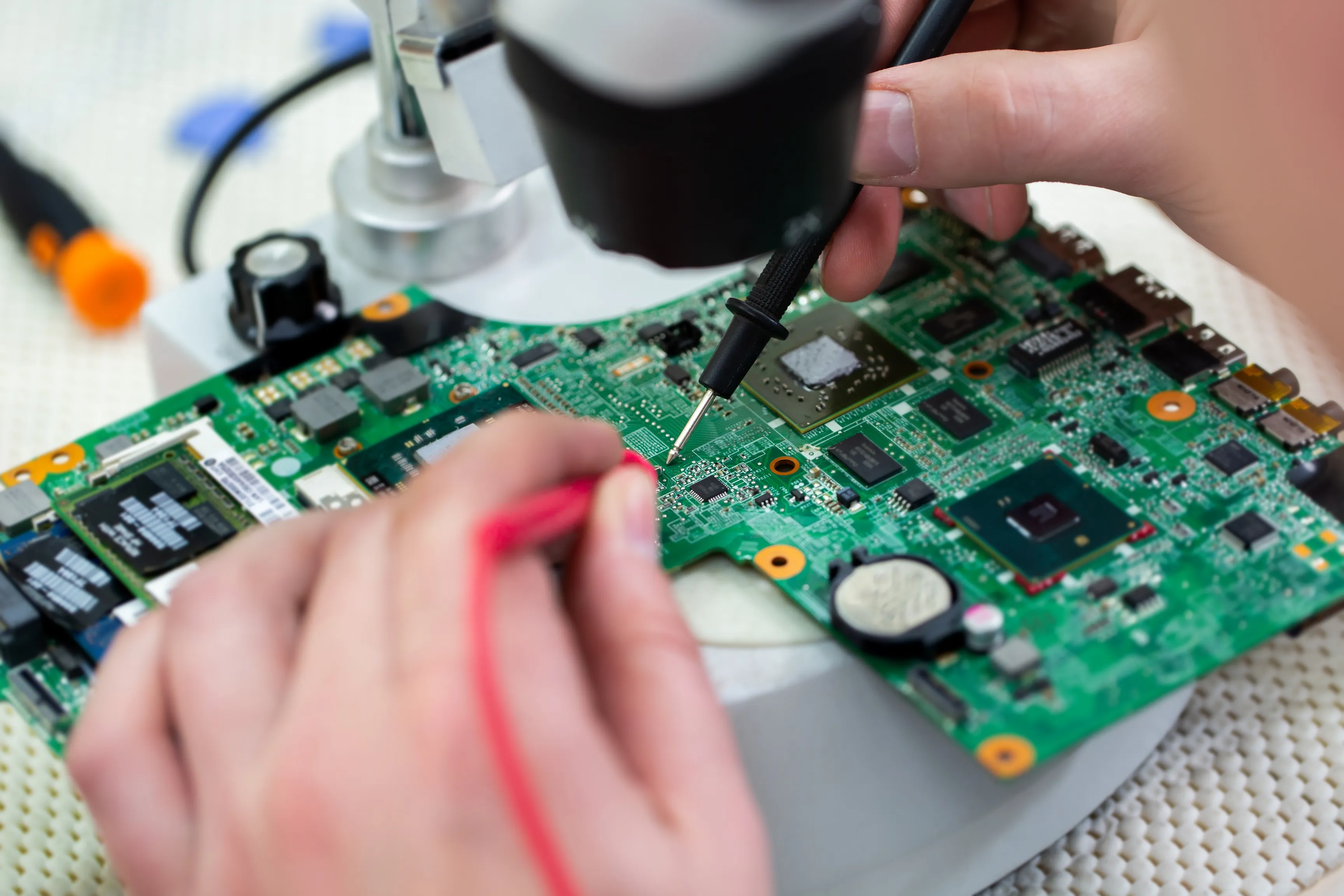
Complete Turnkey Solutions
20+ Years of Experience
Customer-Centric
Cost-Effective Manufacturing
Scalable Manufacturing
State-of-the-Art Technology
BGA Rework & Reballing: Precision Solutions for Complex PCB Repairs
At Surface Mount Solutions (SMS), we offer specialized BGA Rework & Reballing services to repair and rework Ball Grid Array (BGA) components on printed circuit boards (PCBs). BGAs are critical components in many modern electronics due to their ability to handle high-speed, high-density connections. However, BGA issues, such as solder joint failures, can lead to significant performance problems or complete malfunction. Our expert BGA rework and reballing services provide a cost-effective solution to repair and restore functionality to your PCBs without the need for full board replacement.
With years of experience in PCB assembly and rework, SMS uses advanced equipment and techniques to ensure precise rework, ensuring that your PCB assemblies continue to function reliably and meet performance specifications. From correcting solder joint issues to reballing entire components, our team is equipped to handle even the most complex rework projects.
What is BGA Rework?
BGA rework refers to the process of repairing or replacing defective Ball Grid Array components on a printed circuit board. This process involves removing the faulty BGA, re-soldering the component, and ensuring functionality. Rework is often required when there are issues with solder joint connections, such as voids, misalignment, or cracks, which can cause electrical problems or signal degradation.
- Precise Removal of Faulty BGAs: Using advanced rework equipment, we carefully remove defective BGA components without damaging the surrounding areas of the board.
- Re-Soldering and Alignment: After removal, we re-solder the BGA with precision, ensuring proper alignment and strong solder joints.
What is BGA Reballing?
BGA reballing is the process of replacing the solder balls on a BGA component that has been removed or reworked. Over time, solder balls can become damaged, corroded, or misaligned, leading to poor electrical connections. Reballing involves cleaning the component, applying new solder balls, and reattaching the component to the PCB. This process restores the BGA to its original functionality, ensuring a strong and reliable connection.
- Solder Ball Removal: The old, damaged solder balls are carefully removed from the BGA using specialized equipment.
- Reballing with Precision: We apply new solder balls to the BGA, ensuring proper alignment and reliable connections.
- Component Reinstallation: After reballing, the BGA is reinstalled on the PCB and ensuring functionality.
Why BGA Rework & Reballing is Critical
BGA components are widely used in modern electronics due to their ability to handle high-performance applications in industries such as telecommunications, aerospace, medical devices, and consumer electronics. However, these components can be prone to failure due to their complex structure and the high density of solder joints. Reworking or reballing these components is often the most cost-effective way to repair a board without replacing the entire assembly. Our BGA rework and reballing services provide a reliable solution for fixing issues such as:
- Solder Joint Failures: Defects in solder joints, such as voids or cracks, can disrupt signal integrity and cause performance issues. Rework and reballing restore these connections.
- Misaligned Components: Misaligned BGAs can lead to improper electrical connections, but rework ensures proper placement and alignment of the component.
- Corrosion and Damage: Over time, solder balls may become corroded or damaged, affecting the performance of the BGA. Reballing replaces the damaged solder balls and restores functionality.
Advanced Techniques for Reliable BGA Rework
At SMS, we use state-of-the-art equipment and advanced rework techniques to ensure precise and reliable results. Our rework process involves using temperature-controlled reflow systems to carefully remove and re-solder BGAs, minimizing the risk of damage to the board and surrounding components. Our technicians are highly trained and experienced in handling even the most delicate rework projects, ensuring that your boards are restored to full functionality.
- Temperature-Controlled Reflow: Our reflow systems use precise temperature control to safely remove and reattach BGA components, preventing damage to the PCB.
- Precision Alignment Tools: We use alignment tools to ensure that each BGA is correctly positioned, reducing the risk of misalignment or faulty connections.
Industries That Rely on BGA Rework & Reballing
Our BGA rework and reballing services are trusted by companies across a wide range of industries where high-reliability PCBs are essential. Whether you’re working on telecommunications equipment, medical devices, or consumer electronics, our rework solutions ensure that your boards are restored to full functionality and ready for use in mission-critical applications.
- Telecommunications: In the fast-paced telecommunications industry, reliable PCBs are essential for maintaining network infrastructure. Our rework services help repair BGAs, ensuring continued performance and reliability.
- Medical Devices: Medical devices rely on flawless operation, and BGA rework ensures that even the most critical components function as intended in life-saving applications.
- Consumer Electronics: From smartphones to gaming consoles, BGA components are central to consumer electronics. Our rework and reballing services help extend the life of these products, reducing the need for costly replacements.
Benefits of BGA Rework & Reballing
Choosing SMS for your BGA rework and reballing needs offers several advantages. Our expert technicians, combined with advanced equipment, ensure that every rework project is handled with precision and care. By choosing rework instead of full board replacement, you save time and money while ensuring your products continue to perform reliably in the field.
- Cost-Effective Repairs: Reworking or reballing BGAs is often far more cost-effective than replacing an entire PCB, helping you save on manufacturing costs.
- Improved Board Reliability: Our rework services restore the integrity of your PCBs, ensuring that they continue to perform reliably in their intended applications.
- Expert Technicians: Our technicians are highly skilled in BGA rework and reballing, ensuring that every project is completed to the highest standards.
Why Choose SMS for BGA Rework & Reballing?
At SMS, we are committed to delivering precise, reliable rework solutions for complex PCB issues. Our BGA rework and reballing services are designed to extend the life of your printed circuit boards, restore functionality, and reduce the need for costly replacements. With decades of experience in the electronics manufacturing industry, SMS is the trusted partner for businesses looking to repair and restore BGAs with confidence.
- Advanced Rework Equipment: We use state-of-the-art rework systems to ensure precise, reliable repairs for even the most complex BGA issues.
- Skilled Technicians: Our team of highly trained technicians ensures that every rework project is handled with care and expertise.
- Proven Results: With decades of experience, SMS has the knowledge and resources to deliver reliable rework solutions for businesses in a wide range of industries.
Get Started with BGA Rework & Reballing
If you're ready to restore functionality to your printed circuit boards and extend their lifespan with expert BGA rework and reballing services, SMS is here to help. Contact us today to learn more about our rework solutions and how we can support your next project with reliable, cost-effective repairs.
Get in touch today to discuss how we can turn your complex designs into reliable, high-quality products.
From quick-turn PCB assembly to full turnkey solutions, our services cover every stage of the manufacturing process. Whether you need expert materials procurement, thorough testing, or final delivery, we ensure each step is handled with precision, efficiency, and quality.
Ensure flawless PCB performance with our functional testing services, designed to verify that every board functions perfectly under real-world conditions.
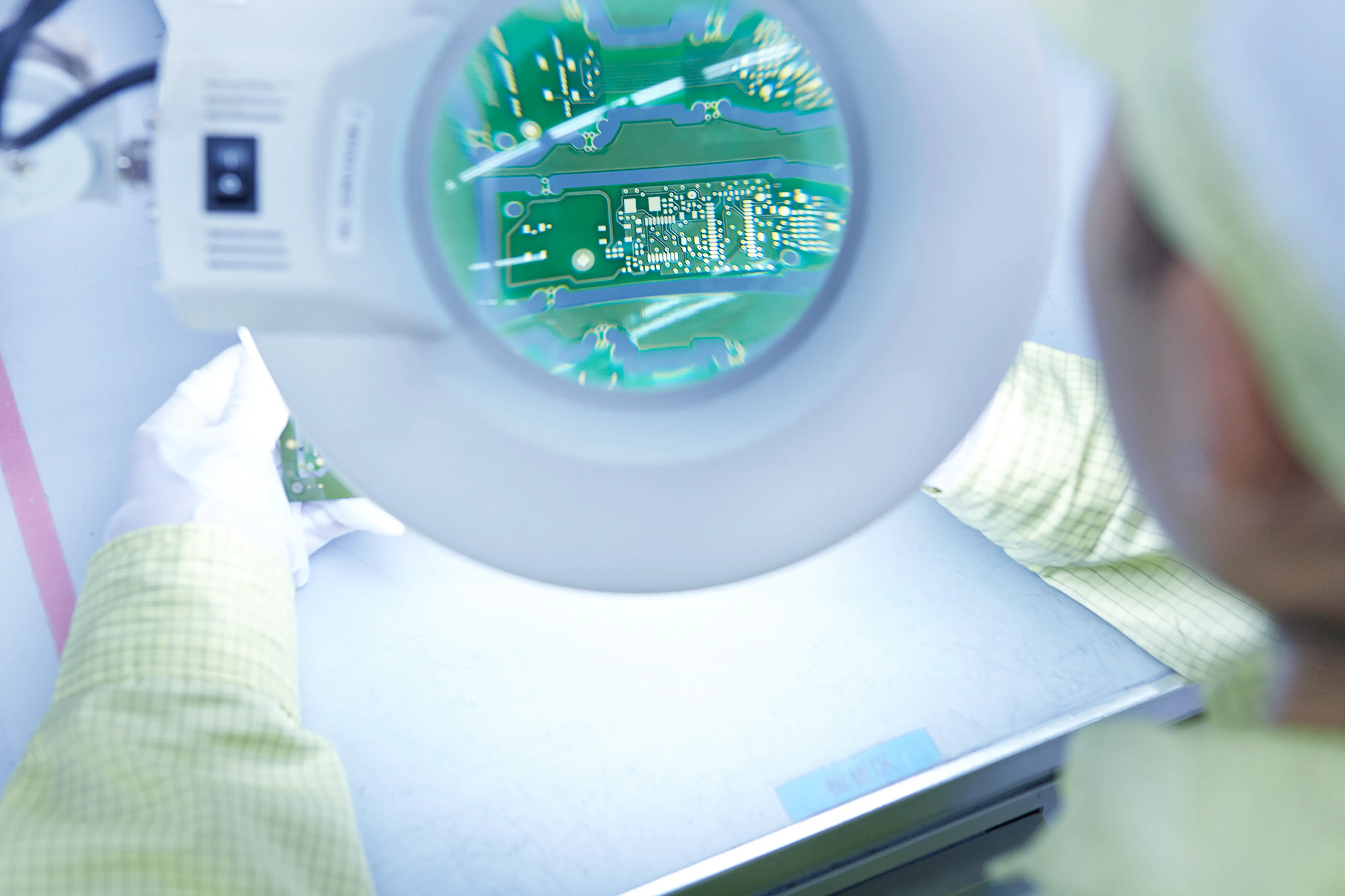
Get fast prototype PCB assembly services for rapid iterations and reliable results, ensuring your project moves quickly through development.
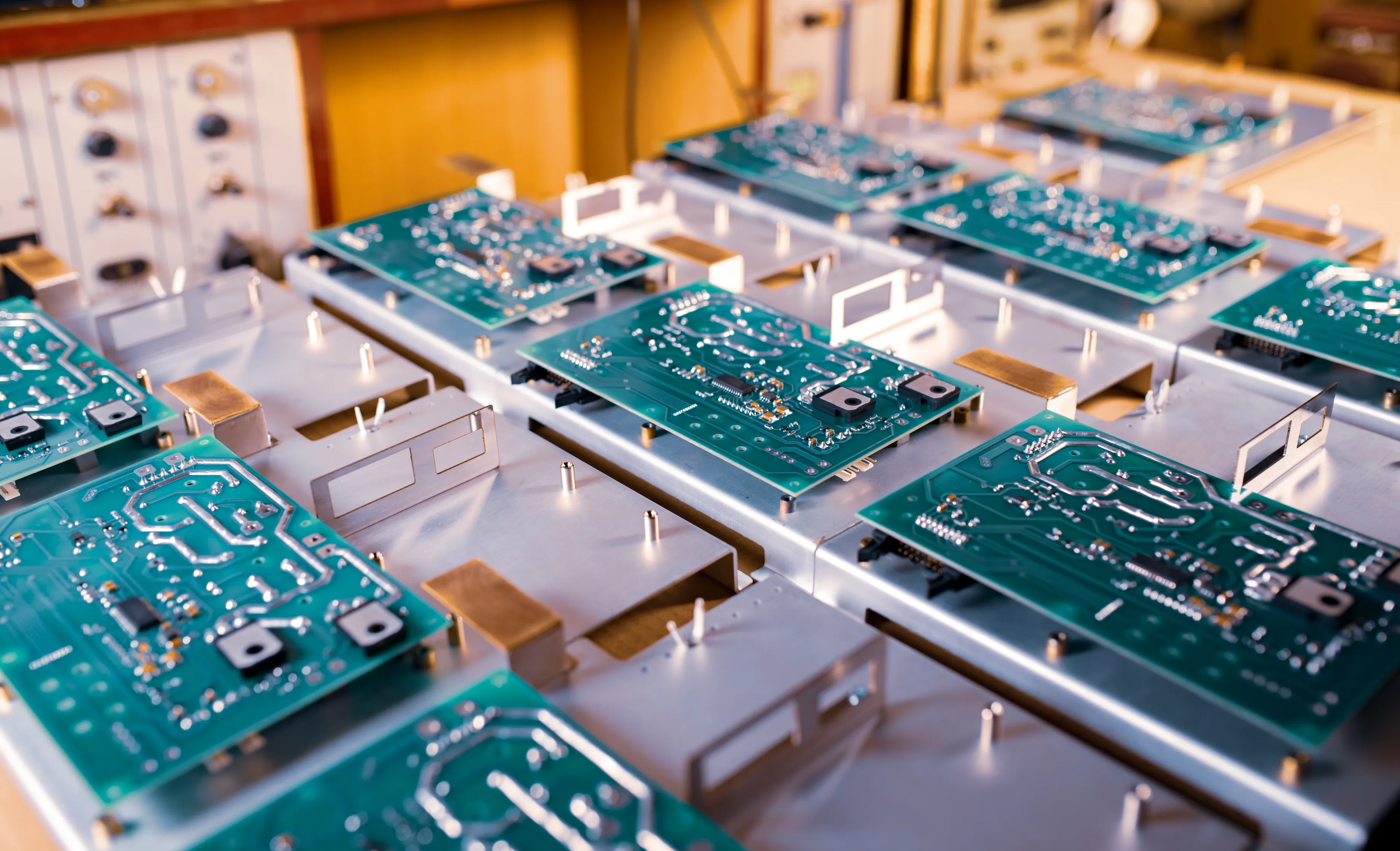
Get precision BGA rework and reballing to ensure reliable PCB connections and long-term performance for your most complex assemblies.
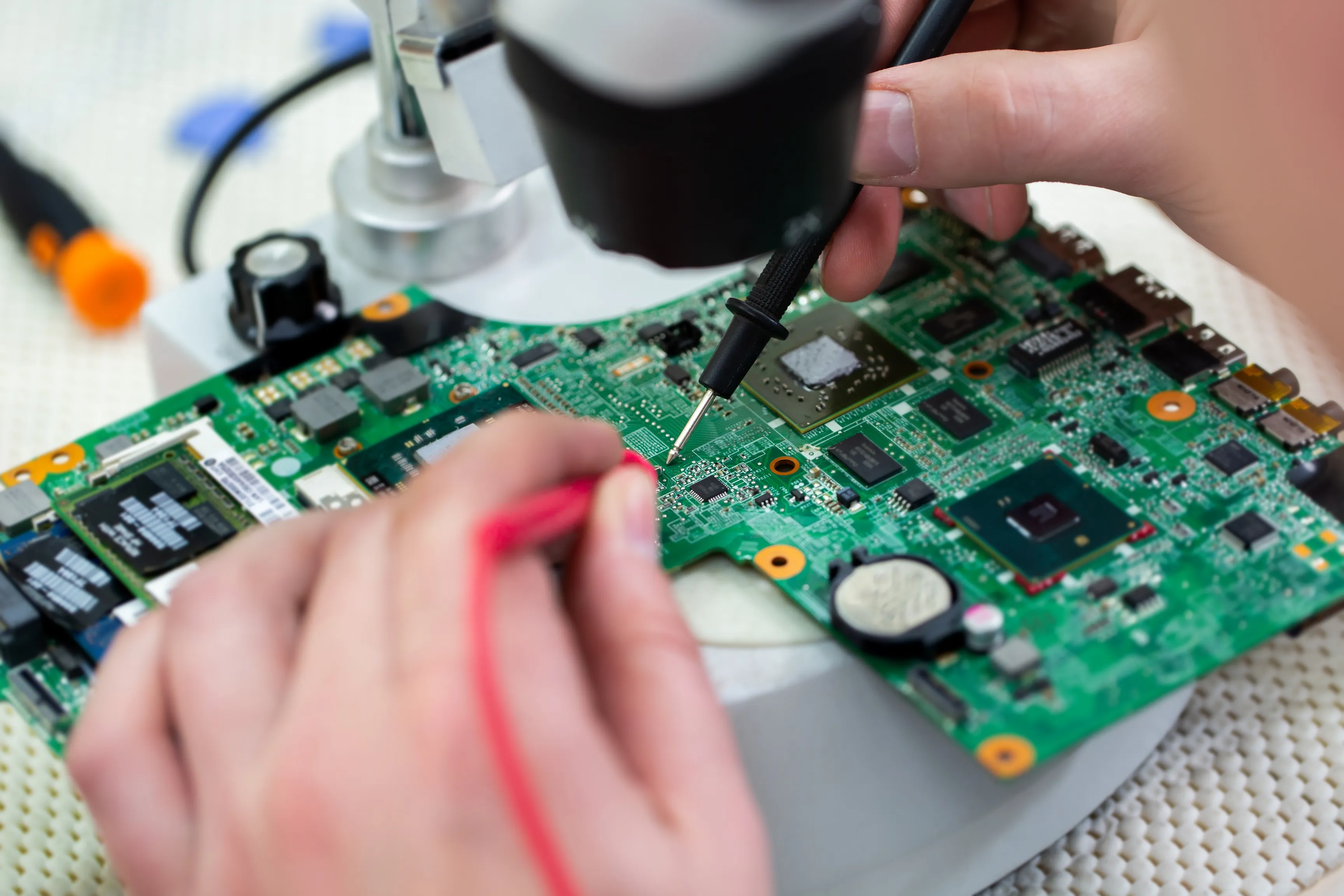
Ensure flawless PCB assembly with our AOI and visual inspection services, detecting defects early and ensuring top-tier quality control.
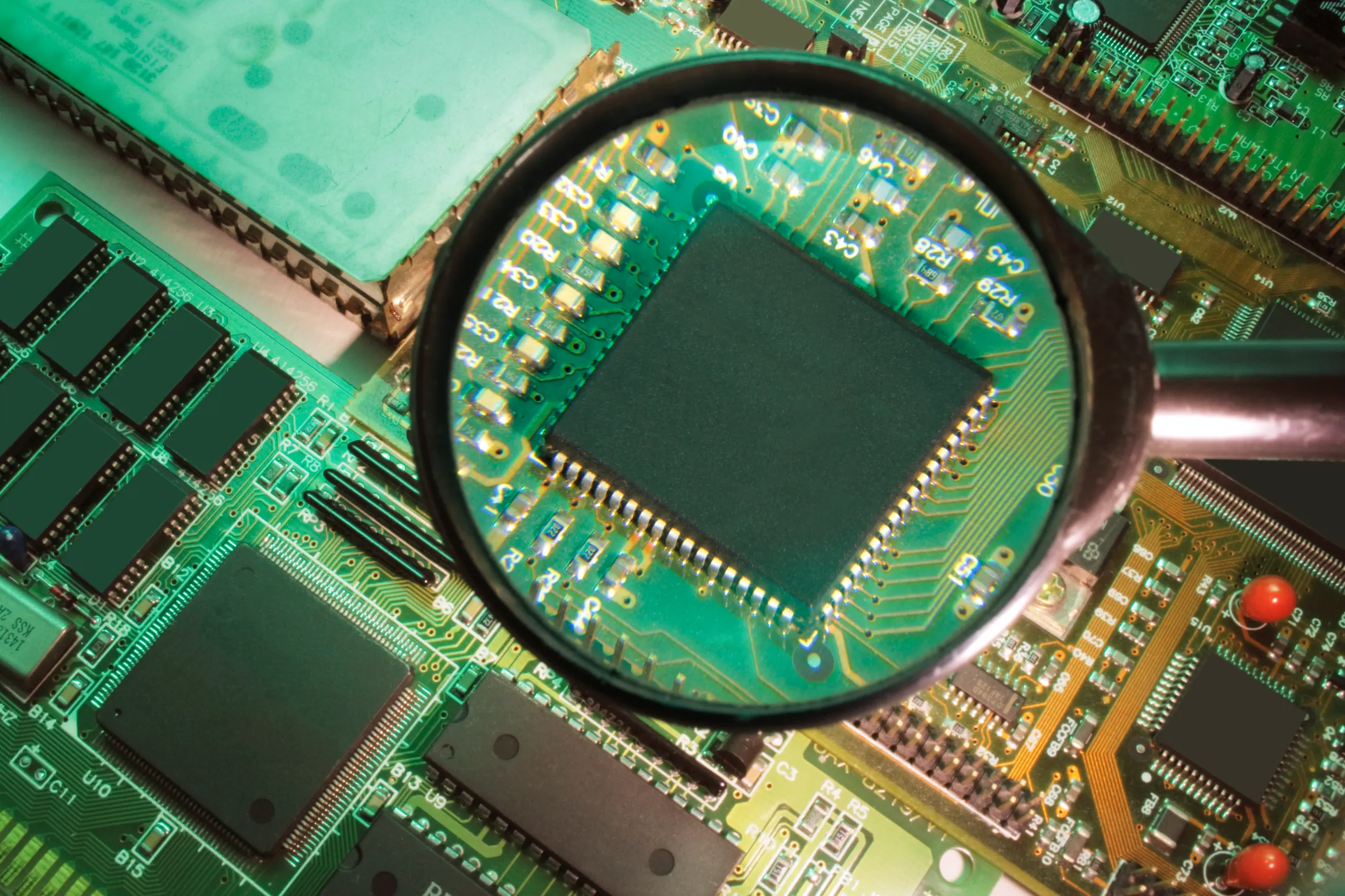
Get contaminant-free boards with our advanced inline aqueous cleaning service, ensuring optimal performance and durability for every project.
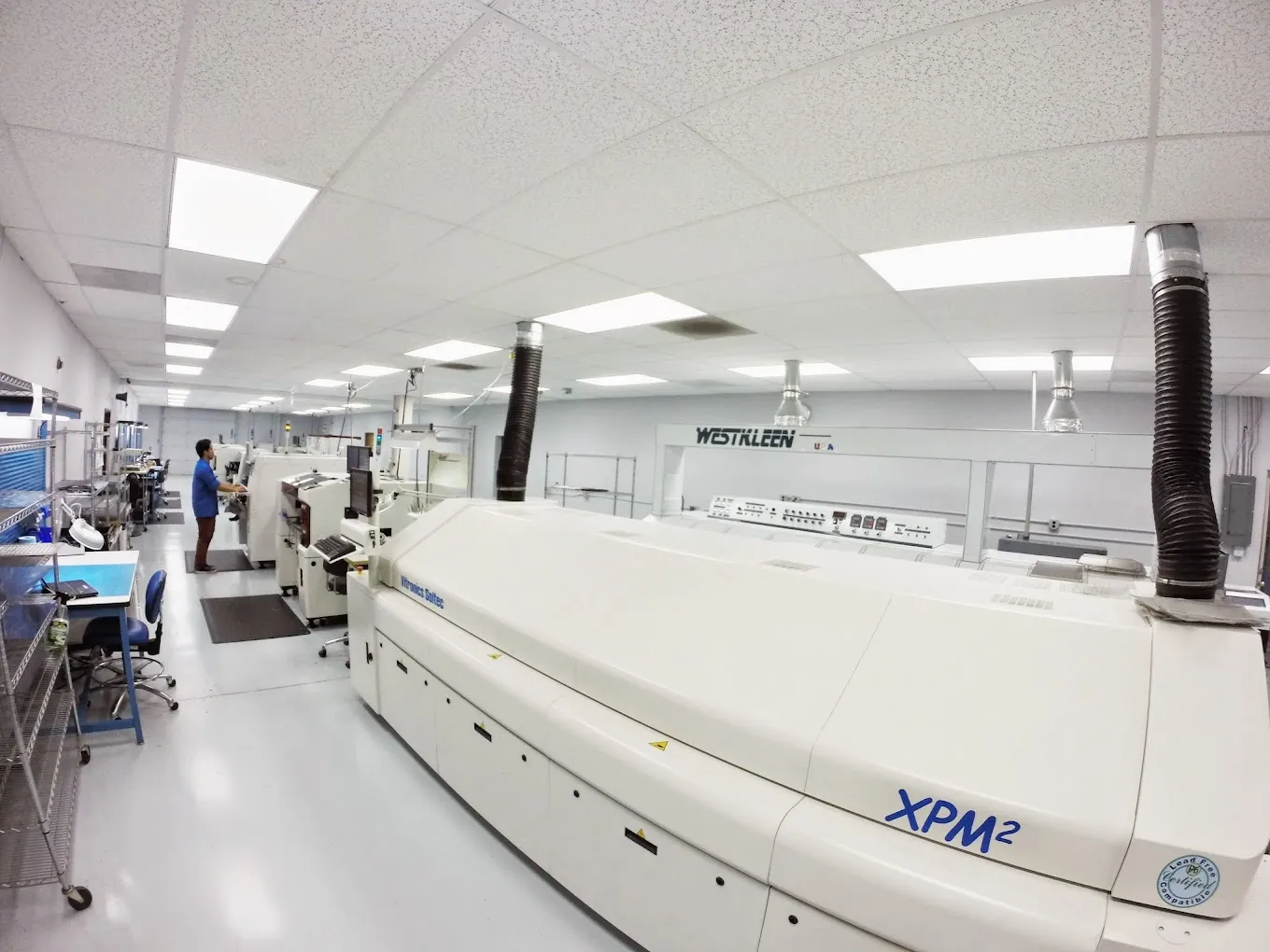
Simplify your project with our turnkey PCB assembly services, handling everything from component sourcing to final delivery.
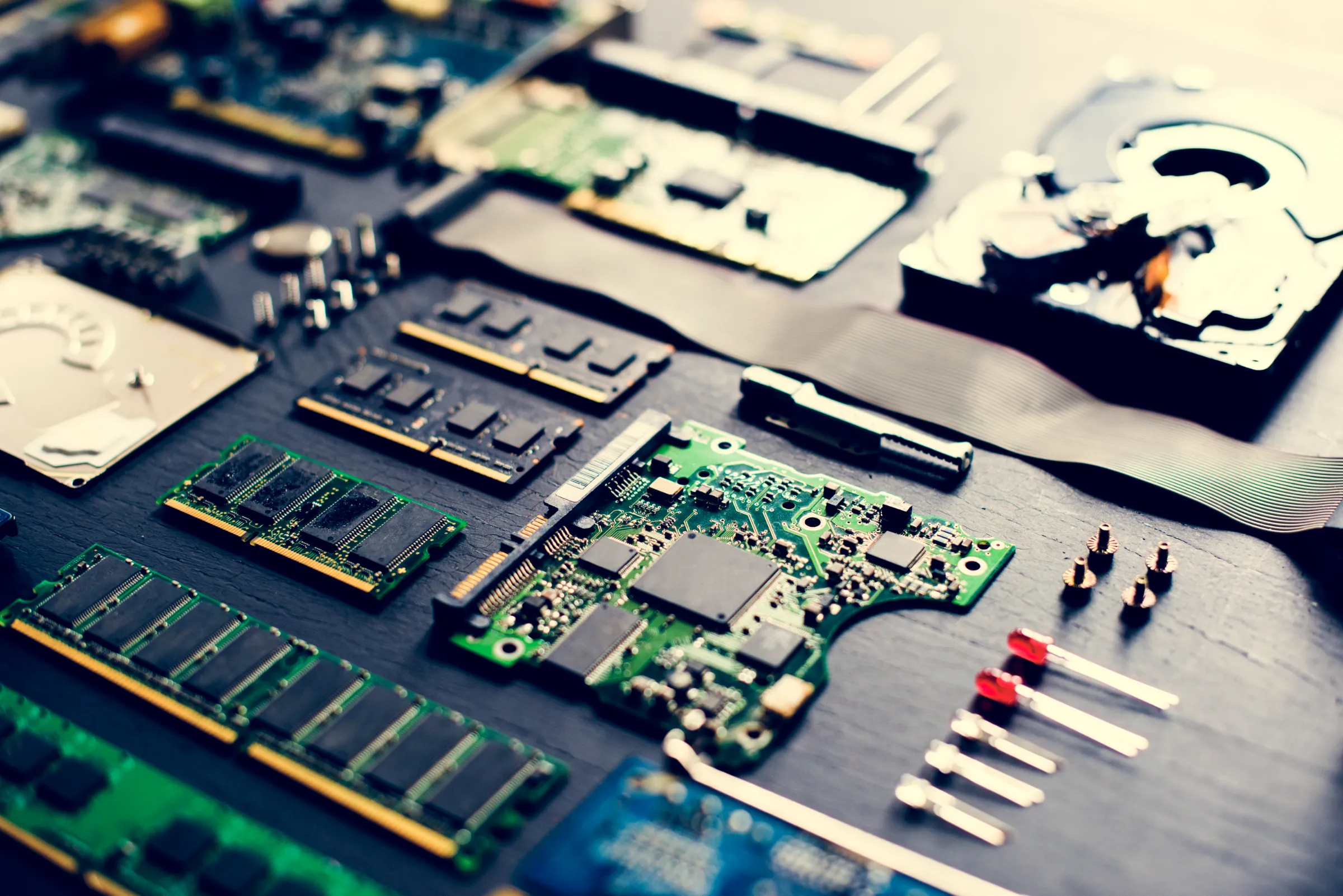
Maintain control by supplying your own components while we handle the assembly, ensuring flexibility without sacrificing quality.
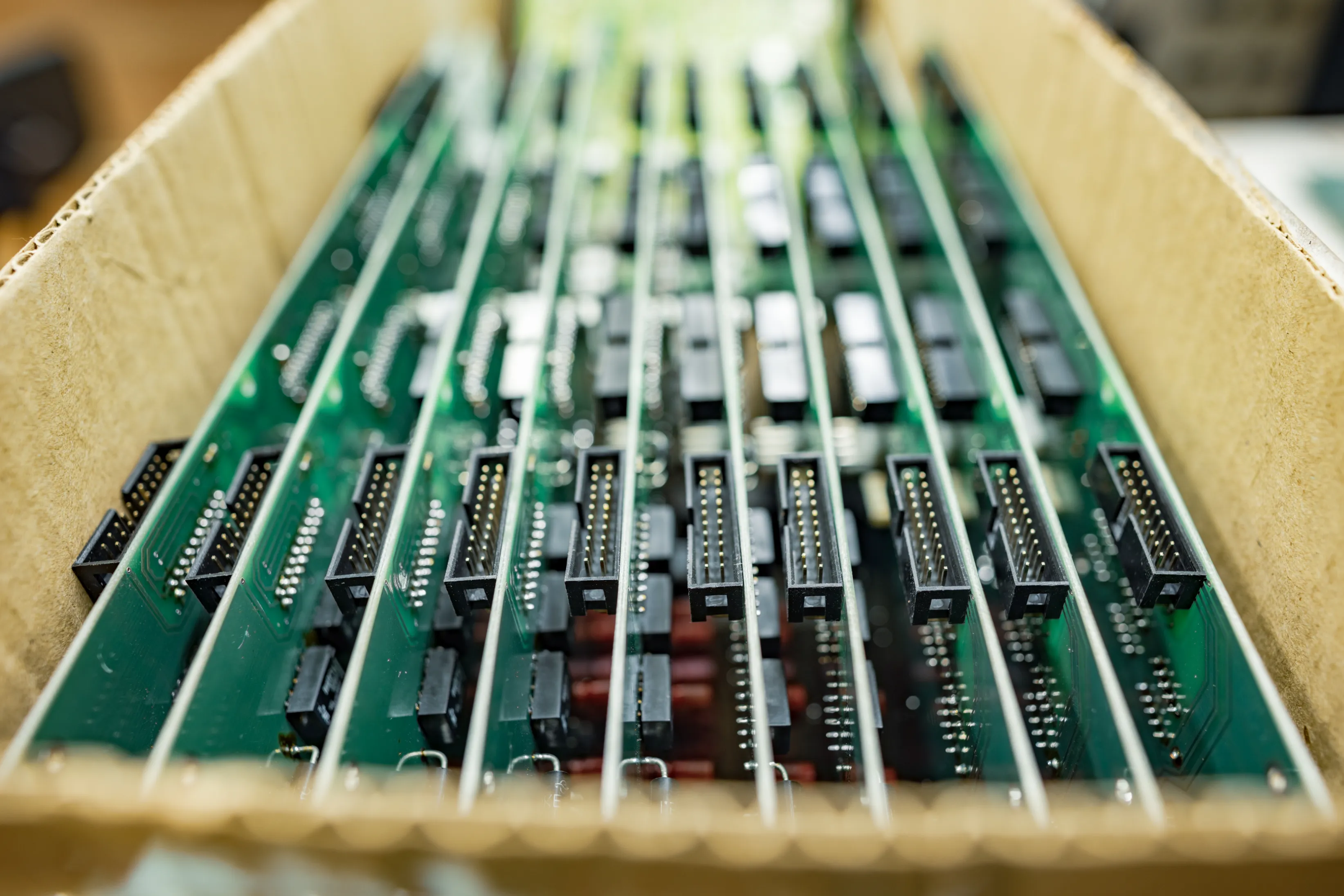
Meet tight deadlines with our high-quality QuickTurn PCB assembly, delivering reliable results in as little as 2-4 days.
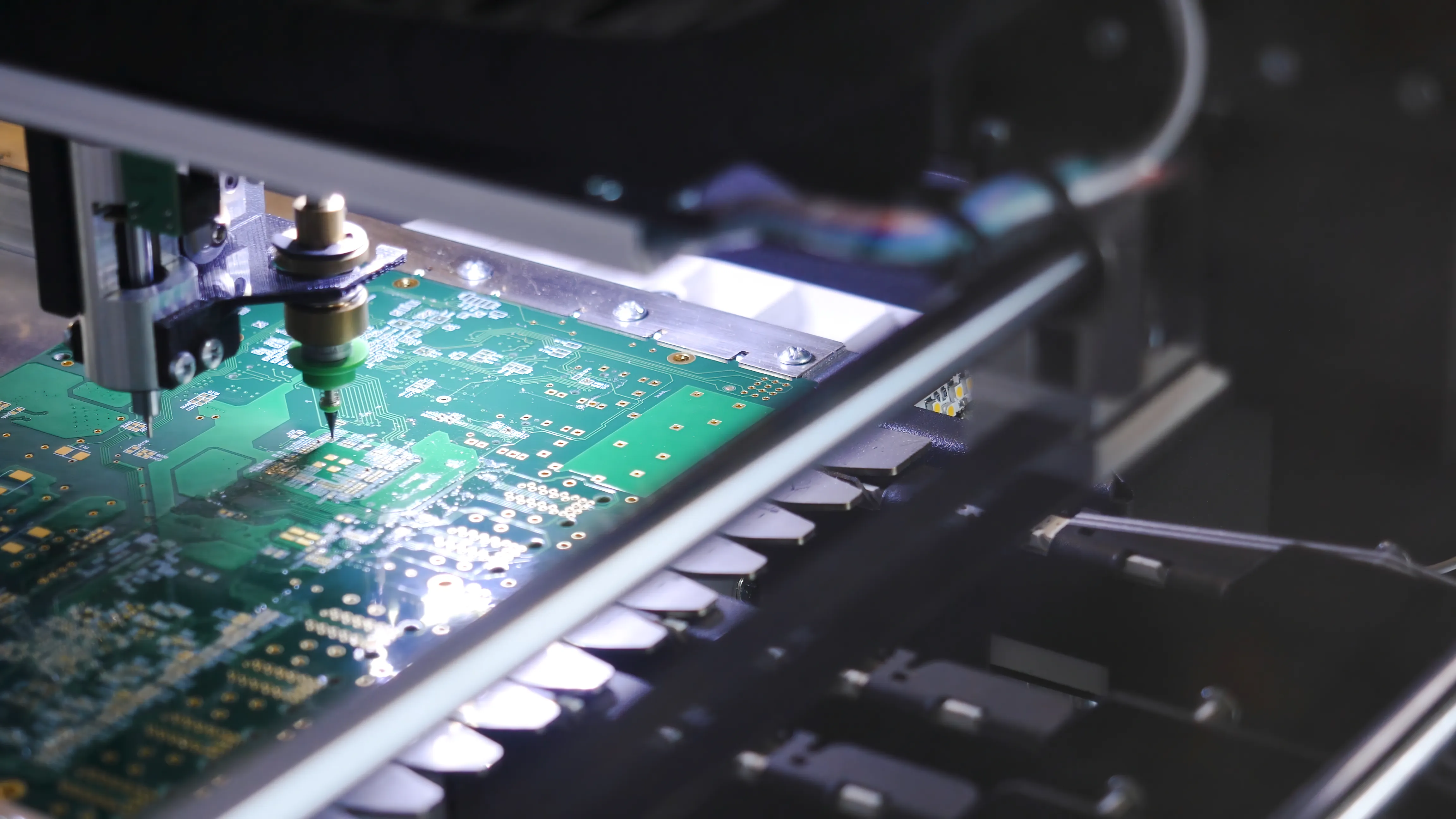
Ensure efficient PCB assembly with reliable materials procurement and kitting. Learn how we streamline the process and keep production on time.
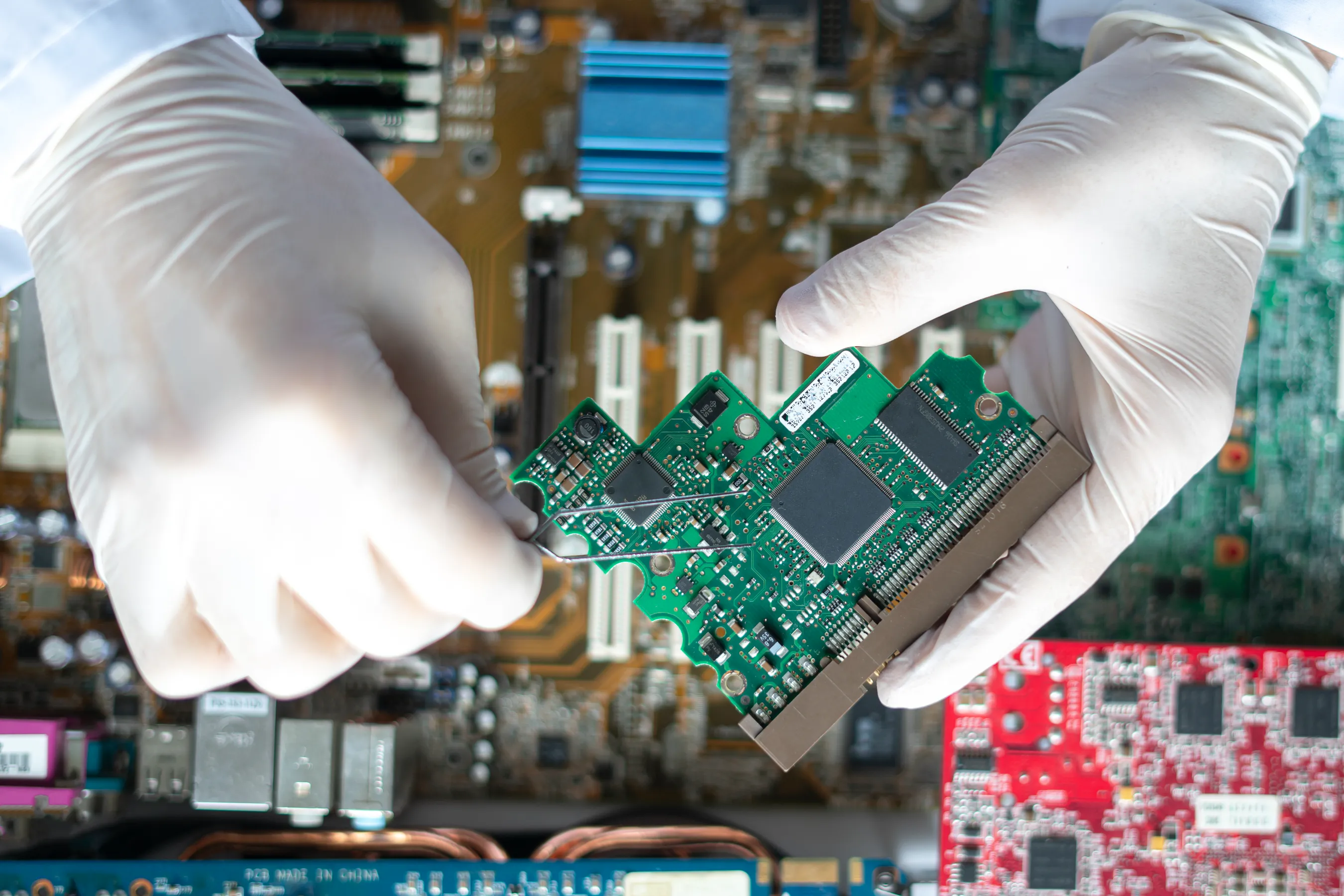
Turning complex circuit board designs into reliable, high-quality products requires an efficient and detail-oriented process. Our step-by-step approach eliminates common manufacturing obstacles, ensuring smooth production, superior quality, and on-time delivery. Each stage is designed to tackle potential pain points, giving you confidence that your PCB assembly project will be handled with precision and expertise.
Every successful project starts with a strong foundation. Our engineers work closely with your team to review your design files, providing Design for Manufacturability (DFM) feedback. This early-stage consultation helps prevent costly revisions and optimizes your design for a seamless transition to production.
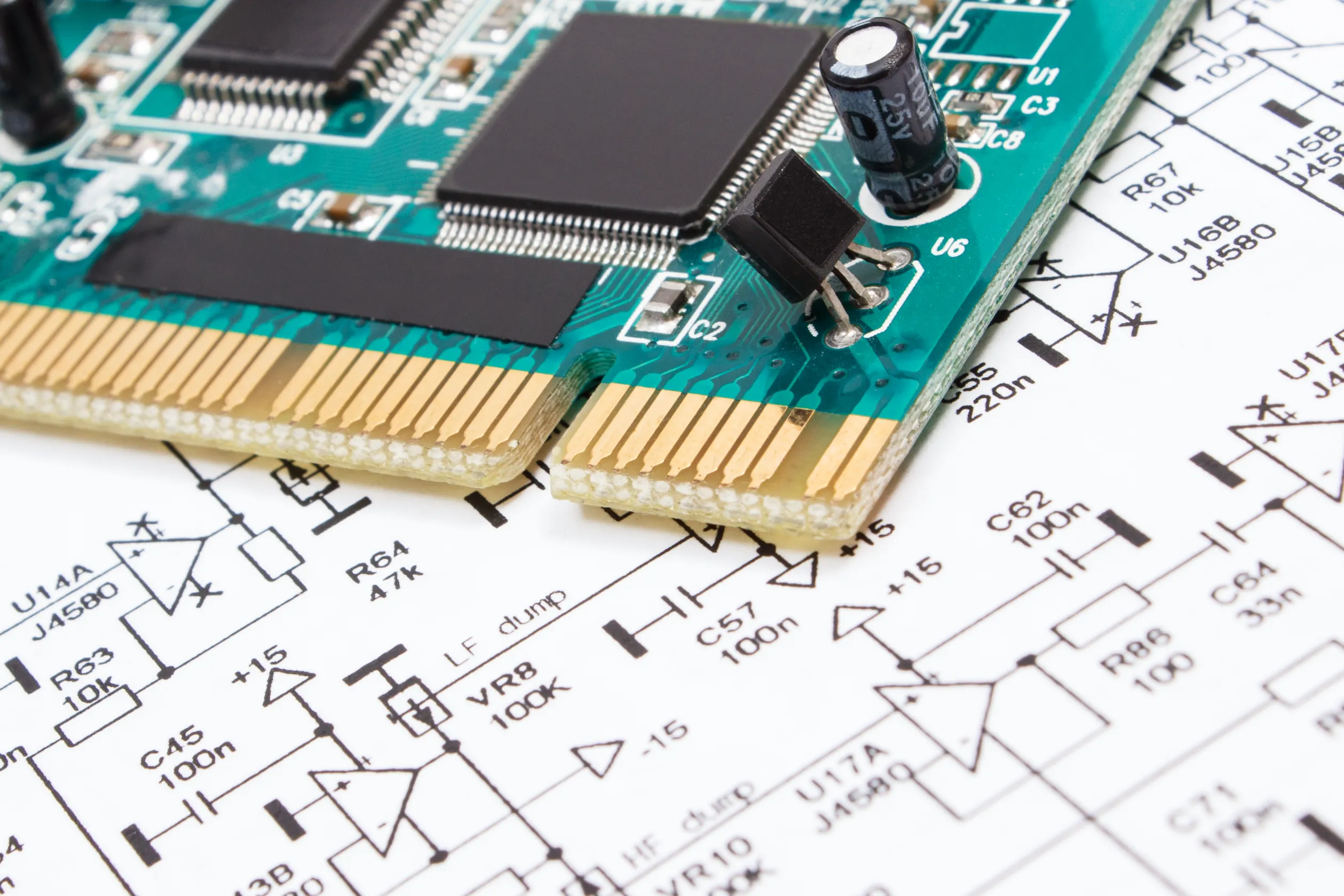
Component sourcing can be challenging, especially when balancing cost and lead times. Our experienced procurement team handles all aspects of materials procurement, ensuring that the best-quality components are used and that your project stays on schedule, even for complex printed circuit board designs.
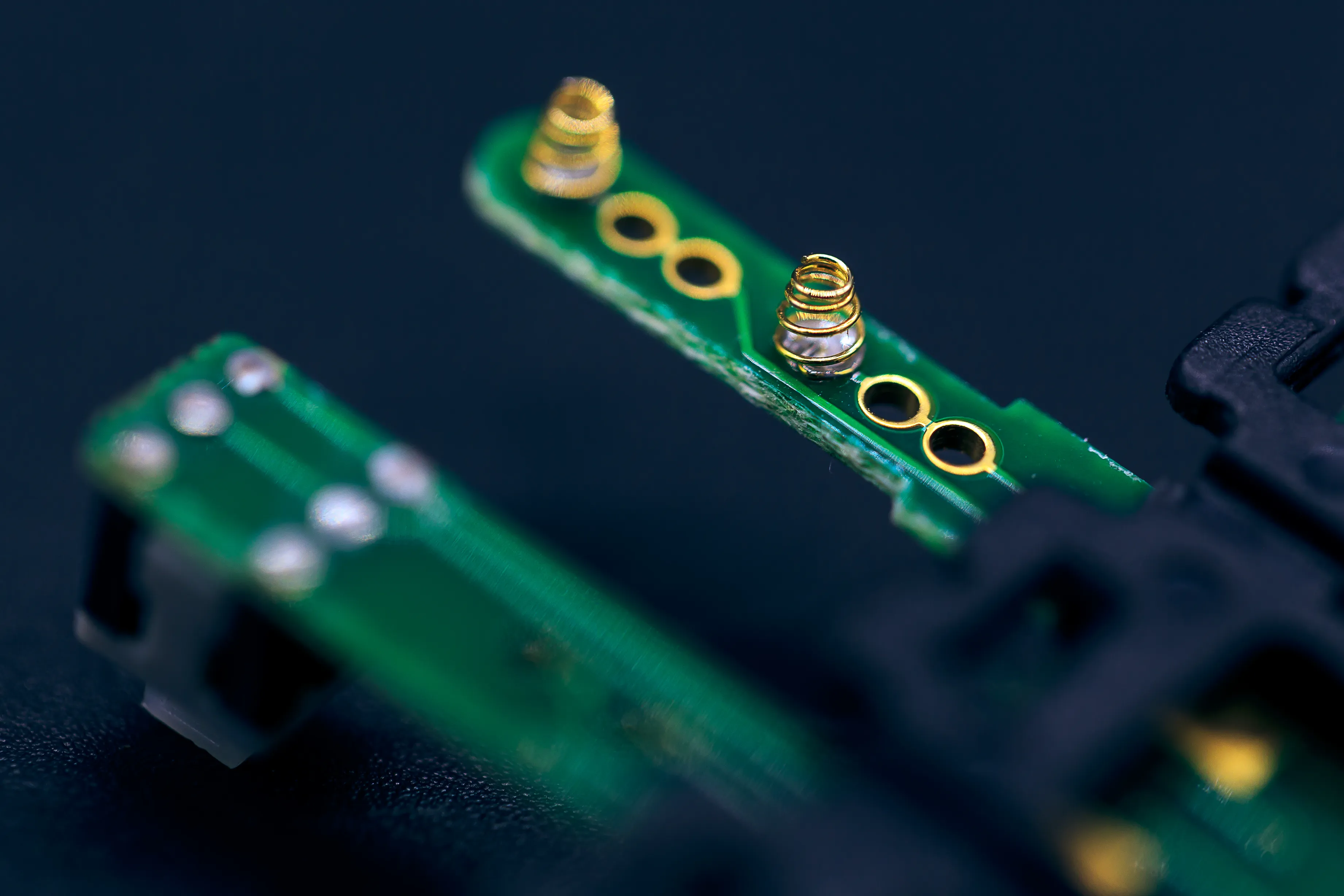
We use state-of-the-art surface mount technology (SMT) and through-hole assembly techniques to build your circuit boards with the highest accuracy and consistency. Our advanced equipment and skilled technicians ensure precise placement of even the smallest components for a robust, reliable build.
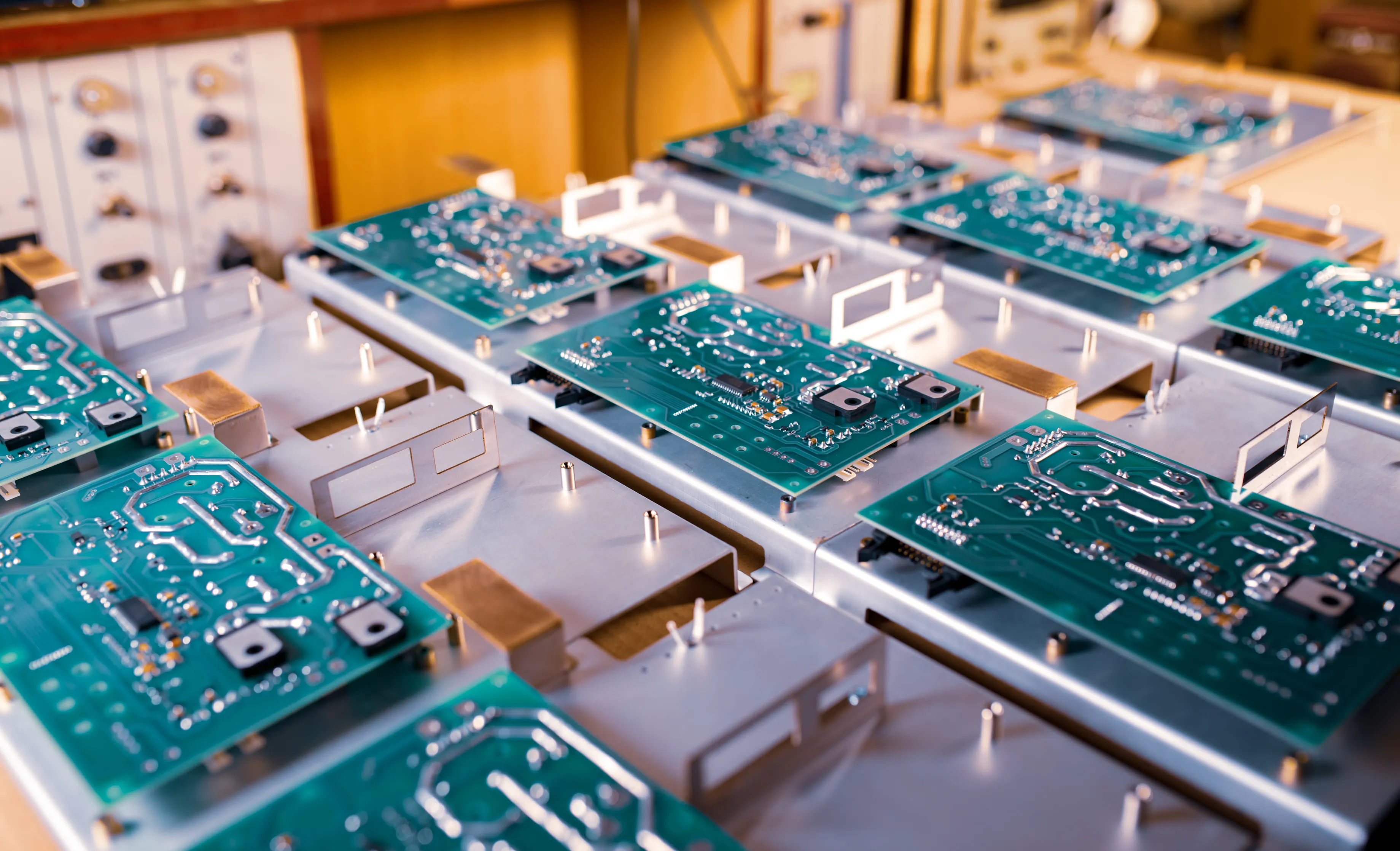
Quality is our top priority. Each assembly goes through multiple inspection stages, including Automated Optical Inspection (AOI), X-ray testing, and comprehensive functional testing. This ensures every circuit board meets stringent standards and performs as expected.
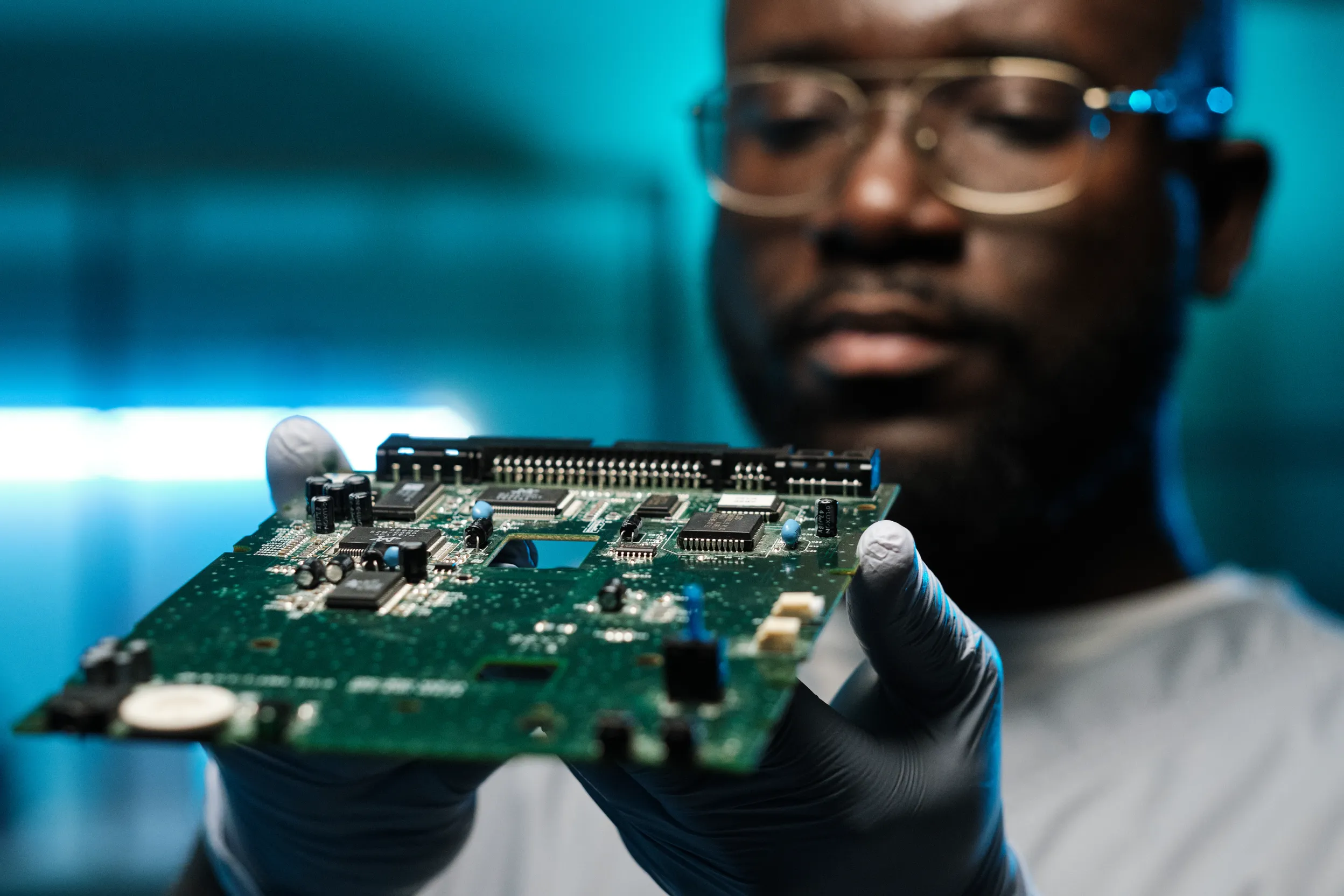
Once testing is complete, your product is prepared for delivery. Whether you need full box builds, special packaging, or local delivery, our logistics team ensures that each project arrives on time and ready for deployment.
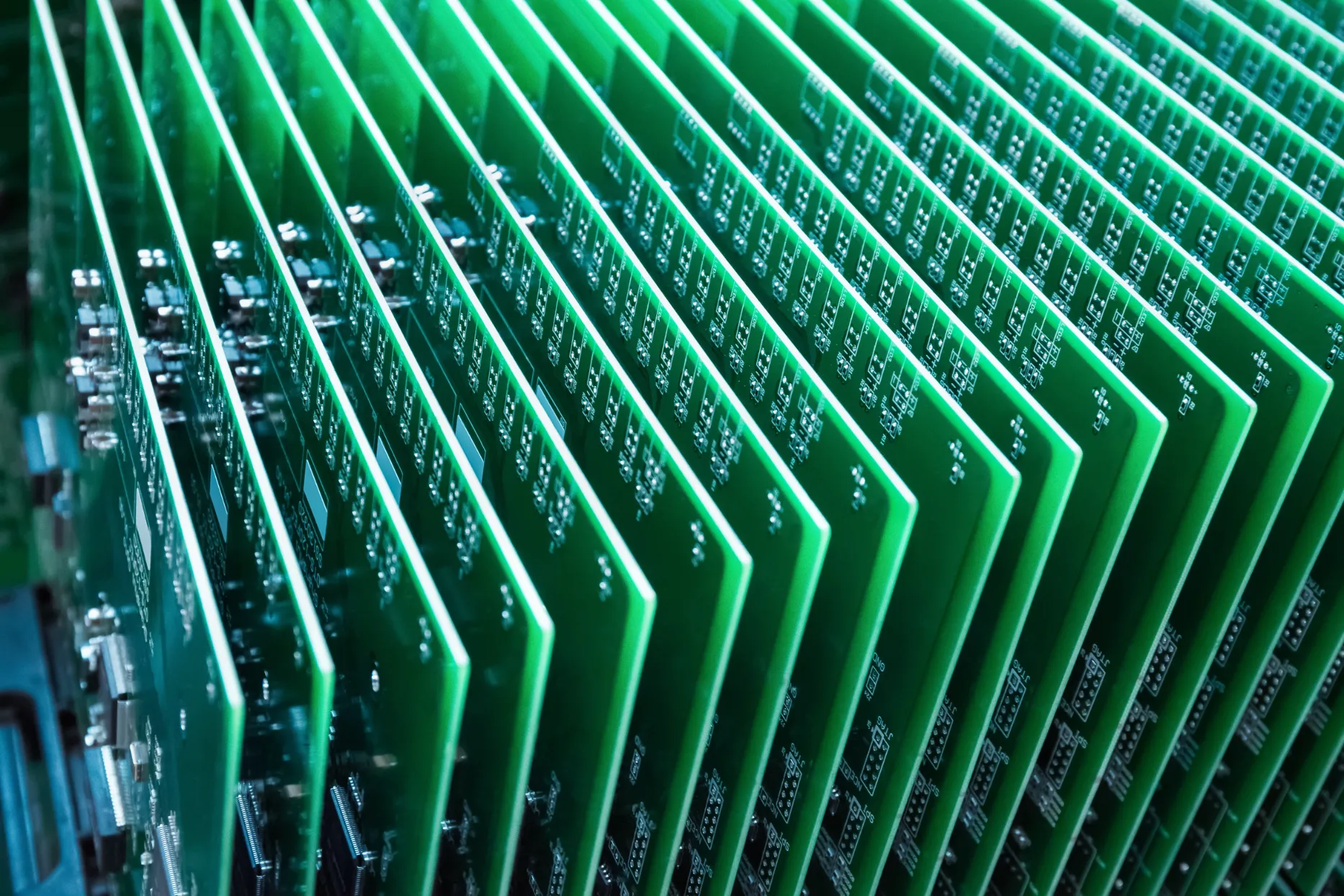
Get in touch today to discuss how we can turn your complex designs into reliable, high-quality products.
Whether you need a quick-turn solution or end-to-end turnkey services, our capabilities are designed to support every stage of your PCB assembly process.
With advanced technologies, flexible lead times, and a commitment to quality, we tailor our services to your specific project requirements.
Depending on customer requests, projects can be completed in as little as 2-4 days, ideal for urgent needs.
A cost-effective solution with a lead time of 5 days (assembly only).
Comprehensive solutions, including procurement and assembly, completed in 10-15 days, depending on part availability.
Advanced SMT capabilities for high-precision components, handling placements down to 01005 with fine-pitch BGA and QFN.
Precision through-hole technology using selective soldering for mixed-technology assemblies, ensuring robust connections.
Accommodating boards up to 18”x15” with custom panelization options for efficient production and cost savings.
Automated Optical Inspection (AOI) and inline cleaning ensure that each PCB assembly is free from defects and contaminants.
Functional testing, BGA X-ray inspection, and rework solutions like BGA reballing to guarantee flawless performance.
Providing full reels and properly labeled components ensures uninterrupted production. Avoid loose parts and supply at least 5 inches of cut tape for feeder compatibility.
See More Details
See More Details
Full Reels Preferred: Whenever possible, provide full reels to minimize machine downtime and ensure uninterrupted production.
Cut Tape: If cut tape is necessary, it must be at least 5 inches long for proper feeder handling.
Machine Loss: Add 2% for all passive components to account for machine loss, and 4% for 0402 caps and resistors.
Loose Components: Loose parts must be hand-placed, which increases time and cost—please avoid whenever possible.
Labeling: Clearly label reels or trays with the customer part number and a complete component description, including value and part type.
IC Packaging: Integrated Circuits (ICs) should ideally be on tape and reel; however, if tubes are used, ensure all components face the same direction and the tube is properly labeled.
Boards must include fiducials, silkscreen reference markers, and adequate component clearance. Consider panelizing for smaller boards to maximize efficiency.
See More Details
See More Details
Fiducials: Boards and panels must include fiducials for accurate alignment during assembly.
Silkscreen: Ensure reference designators and polarity markers are visible on the silkscreen.
Component Clearance: Components should not be placed within 0.080 inches of the edge of the board to avoid damage.
Panelization: For boards smaller than 3x4 inches, consider panelizing. Ideal panel size is approximately 8x10 inches with a 0.25” border.
Double-Sided Boards: For double-sided assemblies, passive components should be placed on the bottom side when possible.
Submit Gerber files, a current BOM, and CAD data for machine programming. Include an audit sheet for any shortages, and consider providing a sample board.
See More Details
See More Details
Gerber Files: Gerber data is required to produce the stencil and ensure proper layout for panelized boards.
BOM (Bill of Materials): Provide an accurate BOM for the current build, including all parts and values, for assembly accuracy.
CAD Data: CAD data is required for machine programming and ensuring precise component placement.
Audit Sheet: Include an audit sheet listing all shortages and discrepancies in the provided parts to avoid delays in the assembly process.
Sample Board (Optional): Providing a sample board can greatly aid in the accurate assembly of your production run.
To guarantee a smooth and efficient assembly process, it's essential to follow these kitting guidelines. By properly preparing your parts, boards, and data, we can ensure accurate and timely production while minimizing delays and errors.
Contact SMS to take advantage of our turnkey PCB assembly services, ensuring fast lead times, precision, and quality.